Crea tus piezas
- participación
En esta sección, sabrá más acerca de nuestro servicio de moldeo por inyección de plástico y descubrirá información directamente relacionada con los procesos de moldeo por inyección.
Elija material
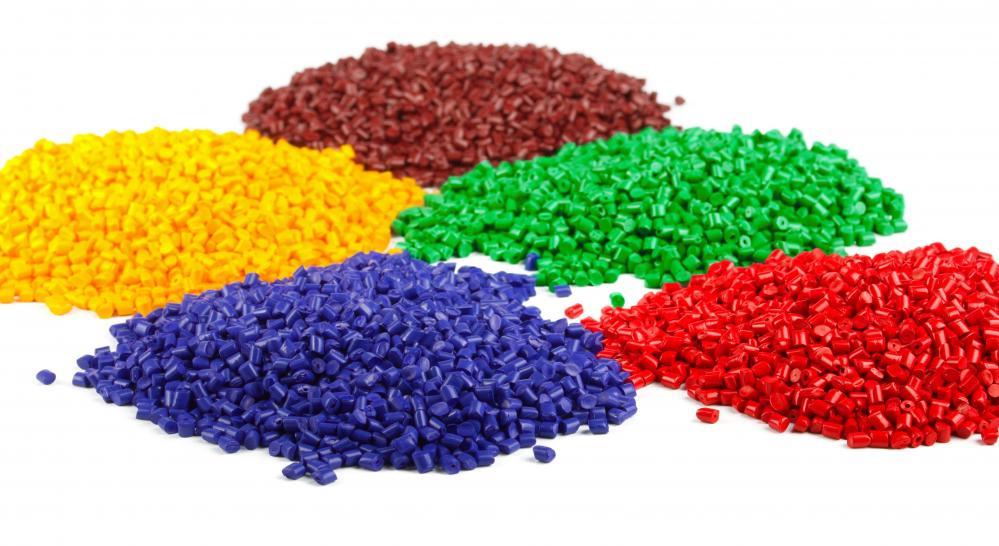
Una selección de los materiales de termoformado personalizados más comúnmente utilizados se enumeran a continuación.
ABS (Acrilonitrilo Butadieno Estireno) : material muy común. Buena rigidez y resistencia al impacto. Disponible en una amplia variedad de colores y varias texturas. Disponible en grados UL94-V0 (ignífugo).
ACRÍLICO (PMMA - Polimetilmetacrilato, Plexiglass) : material resistente al agua y a la abrasión. Fáciles de fabricar Disponible en grados de impacto modificado. Muchos colores disponibles
HDPE (Polietileno de Alta Densidad) : excelente impacto y resistencia química. Buenas propiedades de temperatura fría. Dimensionalmente no es tan estable como otros materiales.
HIPS (poliestireno de alto impacto) : Bajo costo, se forma fácilmente. Disponible en muchos colores. Más quebradizo que ABS.
KYDEX (mezcla de PMMA / PVC) : buen material de uso general, que ofrece un excelente impacto y resistencia química en una lámina altamente cosmética. La mayoría de las calidades son ignífugas para UL94-V0. Disponible en muchos colores y texturas.
PC (policarbonato) : resistencia al impacto muy alta. Claro. Resistencia a altas temperaturas.
PEI (Polieterimida, Ultem) : material de muy alta temperatura. Autoclavable. Color ámbar natural.
PETG (tereftalato de glicol de polietileno) : transparente, con excelente resistencia al impacto. Forma bien
PP (polipropileno) : excelente resistencia química. Rígido, con muy buena resistencia al impacto. Bueno a temperaturas más altas. Pero dimensionalmente no es tan estable como otros materiales, similar al HDPE.
PVC (cloruro de polivinilo) : material rígido. Muy buena resistencia al impacto. Retardante de llama. Disponibilidad limitada.
TPO (poliolefina termoplástica) : propiedades de impacto sobresalientes. Disponible con un acabado de alto brillo. Bueno para aplicaciones al aire libre. Más difícil de formar, especialmente formas de dibujo profundo.
Otros materiales especiales están disponibles, solo contáctenos.
Equipo
Maquinaria de moldeo por inyección
Las máquinas de moldeo por inyección, también conocidas como prensas, consisten en una tolva de material, un pistón de inyección o un émbolo de tipo tornillo y una unidad de calentamiento. Los moldes se sujetan al plato de la máquina de moldeo, donde se inyecta plástico a través del orificio del bebedero para crear moldes de inyección.
Las prensas se clasifican por tonelaje, que es el cálculo de la cantidad de fuerza de sujeción que la máquina puede ejercer. Esta fuerza mantiene el molde cerrado durante el proceso de moldeo por inyección. El tonelaje puede variar desde menos de 5 toneladas a 6000 toneladas, con las cifras más altas utilizadas en comparativamente pocas operaciones de fabricación. La fuerza total de sujeción necesaria está determinada por el área proyectada de la parte personalizada que se está moldeando. Esta área proyectada se multiplica por una fuerza de sujeción de 2 a 8 toneladas por cada pulgada cuadrada de las áreas proyectadas. Como regla general, se pueden usar 4 o 5 toneladas / in para la mayoría de los productos moldeados por inyección. Si el material plástico es muy rígido, se requerirá más presión de inyección para llenar el molde, por lo tanto, se necesita más tonelaje de sujeción para mantener el molde cerrado. La fuerza requerida también puede determinarse por el material utilizado y el tamaño de la pieza, las piezas de plástico más grandes requieren una mayor fuerza de sujeción.
Hoy en día, las prensas eléctricas se están apoderando de las máquinas de inyección hidráulica típicas. Las empresas que producen moldes de inyección los prefieren, ya que ofrecen un 80% menos de consumo de energía y casi un 100% de repetibilidad, mediante el uso de servomotores eléctricos. Mientras que el costo de una máquina de moldeo eléctrico es típicamente un 30% más alto que una prensa hidráulica, la mayor demanda de moldes de inyección está cerrando la brecha en el costo. Se estima que en los próximos 20 años las máquinas de moldeo hidráulico serán una cosa del pasado, ya que más empresas de moldeo están haciendo el cambio para seguir siendo competitivas.
Tenemos 80-3000tons máquinas de inyección de plástico, podemos cumplir sin importar cuán pequeños y grandes sean los tamaños para los clientes, podemos proporcionarle las piezas en 10 días o menos.
¿Cómo funciona el moldeo por inyección?
Los gránulos de material para la pieza se introducen a través de una tolva en un barril calentado, se funden usando bandas calefactoras y la acción de fricción de un barril de tornillo alternativo. El plástico se inyecta luego a través de una boquilla en una cavidad de molde donde se enfría y se endurece a la configuración de la cavidad. La herramienta del molde está montada sobre una placa móvil: cuando la pieza se solidifica, la placa se abre y la pieza sale expulsada utilizando los pasadores de expulsión.
Después de diseñar un producto, generalmente por un diseñador industrial o un ingeniero, los moldes son fabricados por un moldeador (o fabricante de herramientas) a partir de metal, generalmente de acero o aluminio, y mecanizados con precisión para formar las características de la pieza deseada.
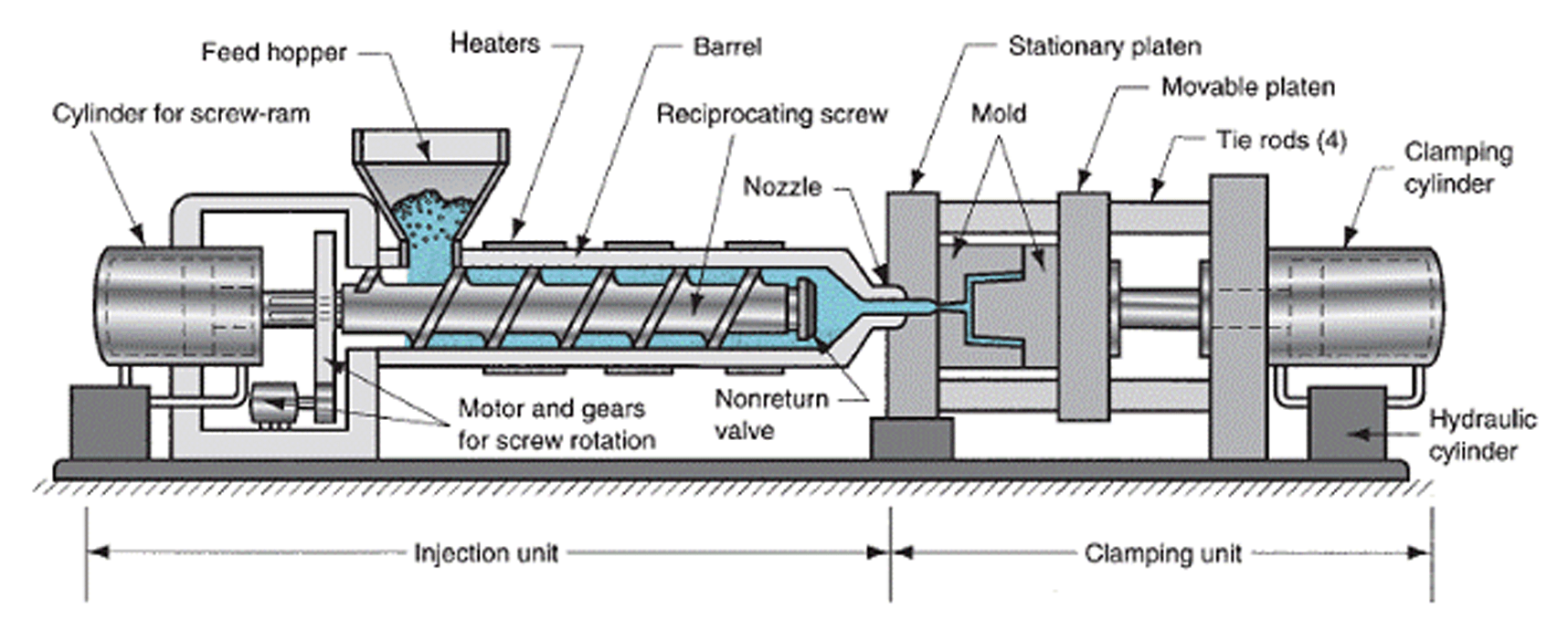
Ciclo de moldeo por inyección
La secuencia de eventos durante el moldeo por inyección de una pieza de plástico se denomina ciclo de moldeo por inyección. El ciclo comienza cuando el molde se cierra, seguido de la inyección del polímero en la cavidad del molde. Una vez que se llena la cavidad, se mantiene una presión de mantenimiento para compensar la contracción del material. En el siguiente paso, el tornillo gira, alimentando la siguiente toma al tornillo frontal. Esto hace que el tornillo se retraiga a medida que se prepara la siguiente toma. Una vez que la pieza está lo suficientemente fría, el molde se abre y la pieza moldeada por inyección se expulsa. Las empresas de moldeo suelen utilizar la siguiente fórmula para determinar el tiempo de ciclo de los moldes de inyección.
Tiempo total = 2M + T + C + E
Dónde:
(2M) = dos veces el tiempo de apertura / cierre del molde
(T) = Tiempo de inyección (S / F)
(C) = Tiempo de enfriamiento
(E) = Tiempo de expulsión (E)
(S) = Tamaño del molde (in3)
(F) = Velocidad de flujo (in3 / min)
El tiempo total del ciclo puede calcularse usando tcycle = tclosing + tcooling + tejection
Los tiempos de cierre y expulsión de las piezas moldeadas por inyección pueden durar desde una fracción de segundo hasta unos pocos minutos, dependiendo del tamaño del molde y la máquina. Los tiempos de enfriamiento, que dominan el proceso, dependen del espesor máximo de la pieza.
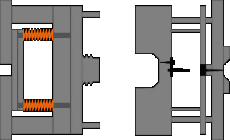
Costo
El costo de fabricar moldes de inyección depende de un conjunto muy grande de factores que van desde el número de cavidades, el tamaño de las piezas (y por lo tanto el molde), la complejidad de las piezas, la longevidad esperada de la herramienta, los acabados superficiales y muchos otros. El costo inicial es excelente, sin embargo, el costo de la pieza es bajo, por lo que con mayores cantidades el precio general disminuye. Con la competencia global, las empresas con un sistema de calidad ISO generalmente tendrán mejores precios, ya que han seguido el proceso y producen menos defectos. Molde Cost Guidline.
Diferentes cavidades del molde, diferentes precios unitarios de la pieza, por supuesto, el costo del molde también es diferente.
Más cavidades de los moldes, más costos serían mayores, pero el precio unitario de la pieza será más económico.
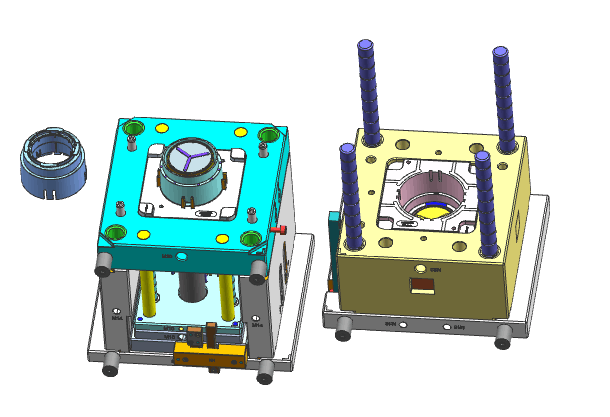
Sigle Cavity (1 * 1)
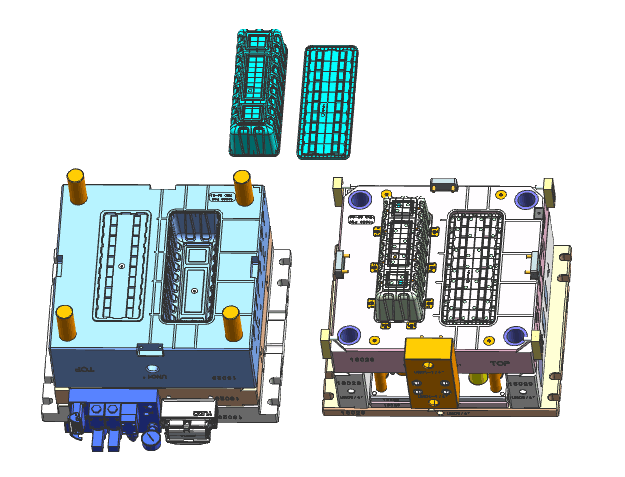
Dos caries (1 * 2)
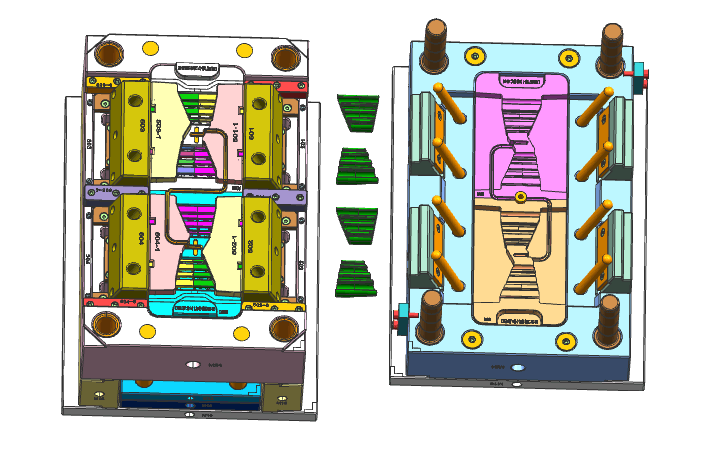
Cuatro caries (1 * 4)